Manuel J. Garcia, President, Spray-Tek, Inc.
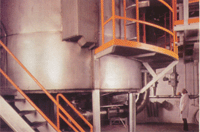
Problem: Spray-Tek, Inc., a custom spray drying company located in Middlesex, NJ, processes products including starches, gelatins, celluloses and gums in continuous production runs of up to four weeks. The plant needs a very dependable homogenizing system that must be flexible to handle a wide composition of emulsion formulations and dispersions.
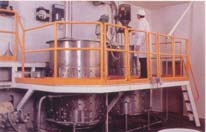
The oil load in emulsions can vary from 10-55% of the total solids. Sometimes the formula requires the addition of fine powders to the emulsion. The presence of lumps or agglomerates in the feed material will cause clogging of the atomizer and disrupt the spray drying operation. Pretesting new formulations is essential from the standpoint of both product quality and efficiency of operation.
Top quality spray dried products must be free flowing and well encapsulated. The dispersed particle size of the emulsion must be controlled within very narrow limits. Spray-Tek's internal quality control criteria is a microscopic evaluation of the batched emulsions. The dispersed particle size profile of the emulsion, when diluted and examined under high power (400-450X), must be smaller than 3 microns, with an allowable limit of several droplets per field of 4 microns.
Solution: A laboratory model reversible homogenizing mixer is used to scale up the necessary parameters for production scale operation. Confidence is established by preparing the exact formula with established processing techniques. Then the emulsion is given a microscopic evaluation.
Laboratory spray drying follows after adjusting the total solids content. Chamber conditions are observed during and after spray drying, and the spray dried product is physically tested. Tests include flow quality, moisture content, microscopic examination and other parameters requested by the client.
The production sequence is started by preparing a concentrated hot emulsifying carrier solution or suspension. This solution is pumped through a bucket strainer into a 750 gallon jacketed stainless steel homogenizing vessel. The dispersed phase is transferred at a controlled rate into the vessel close to the turbine of the production size reversible homogenizing mixer.
The reversible homogenizing mixer is operated in the upward "umbrella" flow mode for very intensive and high shear mixing action. The completed emulsion is sampled and examined microscopically to determine the dispersed particle size profile. Emulsification is continued if profile criteria is not met, and the emulsion is again examined for suitable profile. Then the primary emulsion is diluted with water to the established total solids concentration.
The finished emulsion is transferred to a 1500 gallon holding vessel for production spray drying runs. The spray drying is started as soon as sufficient emulsion is available for continuous operation. After the initial emulsion is prepared and transferred to the holding vessel, the routine in preparing additional emulsions is rapid and exceeds the spray drying capacity of the dryer.
When the formula requires the addition of fine powders to the emulsion, the homogenizer is reversed and operated in the downward "vortex" mode as the fine powder is slowly added. The rotor sucks the powder down into the mixing head where it is subjected to intense mechanical force and hydraulic shear. To ensure a well dispersed system, the homogenizer is reversed to the upward "umbrella flow" and operated for 5-10 minutes. A sample of the finished "emulsion dispersion" is visually inspected by preparing a thin film on a spatula before being transferred for spray drying.
Results: Spray-Tek, Inc., is very pleased with the trouble-free operation of the reversible homogenizing mixers. No major maintenance has been required for a period of four years of continuous operation. Furthermore, quality control of the emulsions and finished spray dried products have been excellent.
Every emulsion processed with the established parameters of formulation and technique has met the quality standards of microscopic evaluation. The reversible homogenizing mixer is both versatile and extremely efficient. Millions of pounds of spray dried products have been manufactured without encountering spray drying problems which are prevalent with substandard emulsification.
Reprinted from November 1986 Chemical Processing